Services
List of Core Services
Kenmark carries out reconditioning of engine components like cylinder heads, exhaust valve spindles and seats (nimonic & stellite), exhaust valve cages/bodies, connecting rods, pistons & crowns, plunger barrels, liners and various types of pumps and other equipment to OEM standards at economical rates.
Diesel engine repairs and maintenance is the core service of Kenmark. Routine maintenance troubleshooting and repairs on all major makes of main and auxilliary engines.
Kenmark provides spare parts for all major engines and other machineries. We can arrange supply of original, OEM, and alternate spares as per the requirement of the vessel / ship owner / manager.
We can supply Main Engine, Aux Engine, Air Compressors, Purifiers, Pumps, Hydraulic Machinery, Navigational Equipment, Automation Equipment and various other spares.
We carry out insitu grinding of crankshafts from pin sizes 120mm and bore. We have sucessfully carried out jobs and salvaged crankshafts to benefit the owners.
Kenmark Tech Solutions is engaged in the O+M of various power plants. Our expertise lies in managing various power plants effectively, right from taking in fuel to delivering power to the exact requirements of the customer. We also manage Sub-Stations connected to these power plants.
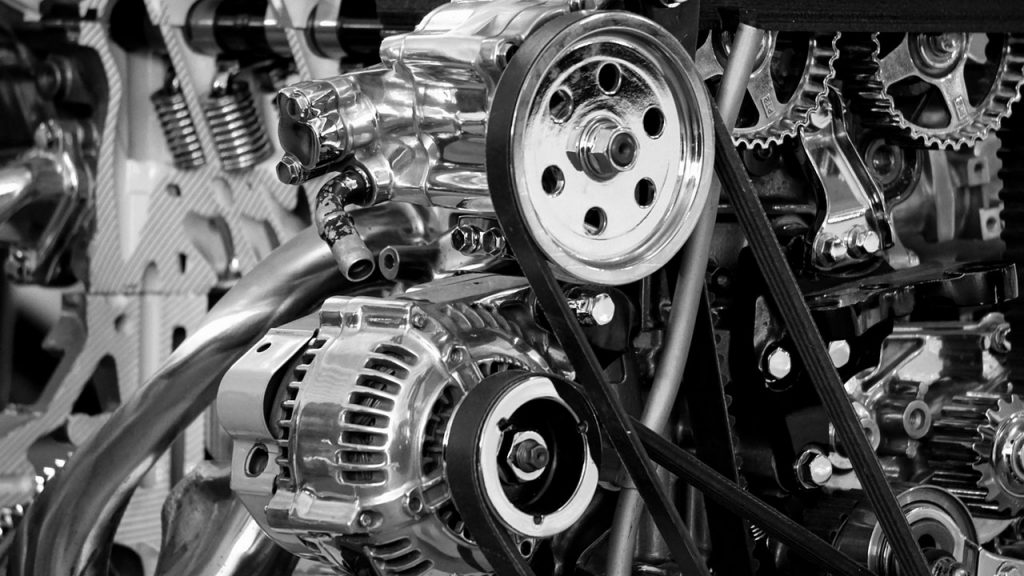
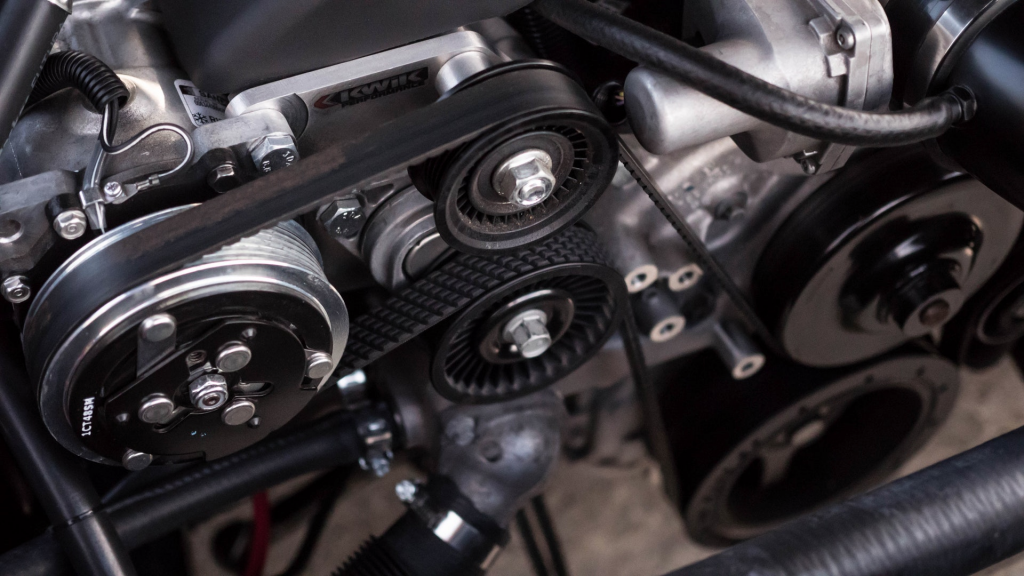
Gives a complete diagnosis of the performance of the engine behaviour. This means that without dismantling various components we can actually find out the health of the engines/components.
Provide third party Inspection / Evaluation services, Condition and monitoring of entire plant, Advice on upgrades, design modifications and plant maintenance programs.
Kenmark is engaged in ship building activity and outfitting of hulls in one of the prestigious yards in INDIA.
Marine – ISM and ISPS systems development, implementation and monitoring.
Industry – Quality Management system to ISO 9001: 2000, CE marking for Pressure Equipment Directive and Quality Assurance system for Products, development, Implementation and Monitoring.
Expertise from retired surveyor of leading classification society.
Diesel Engines can be safely converted to Dual Fuel Technology for the following reasons:
a. To extend the tank capacity of liquid fuel. Gas as back up fuel.
b. To save on the high cost of liquid fuel
c. To control emissions
CTI has developed its patented shields repair for condenser and heat exchanger tubes in 1976. The repair technique involves the installation of thin waited alloy inserts into the damaged ends.
This repair method can save from 75% to 90% versus the cost of traditional retubing.
The shield, besides restoring the tube end erosion / corrosion, will restore tube-to-tubesheet hole integrity, permit proper mechanical tube cleaning and in many cases restore leaking, plugged tubes to full operation.
Once expanded-either mechanically or Hydraulically or a hydrid of the two, the shields then become integral with the parent tubes.
CTI has also developed the technology for repairing failed or plugged tubes with FULL length Liners.
CTI has installed more than 5 million shields, in 32 countries round the world. Savings in cost, practically nill down time of the plant and life extension are some of the benefits.